
With EVs now the undisputable future of motoring, it’s worth examining what is happening in the world of the vehicle’s most important component: the battery.
As manufacturers scramble to secure substantial supplies of vital minerals and materials to keep EV production plans on track, the worldwide battery ‘scene’ evokes the gold rushes of the late 19th century – when hopeful miners sought their fortune.
But what lessons are being learned in the current EV market about batteries and how are their manufacture and management changing, both in terms of how they’re made and how easily they can be repaired, repurposed and recycled? What are the insurance implications for EV users about batteries and is that likely to change? How significant are battery passports and what’s behind the swell of new gigafactories and battery health specialists?
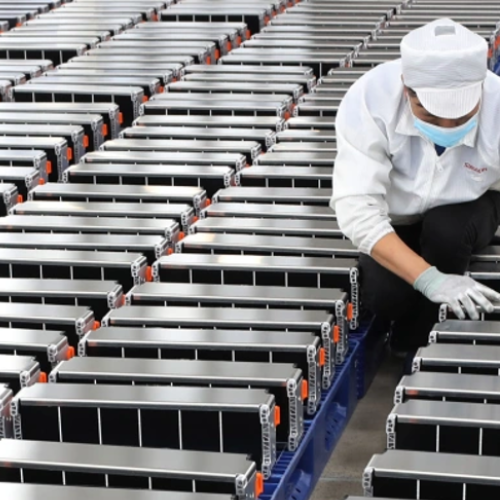
Inside the battery
Most new EVs today use battery technology that’s pretty uniform: hundreds of individual lithium-ion cells packed into modules to make one big power source. Other materials needed to make one include cobalt, graphite, copper, aluminium and steel.
Making batteries is not easy, the materials are hard to access and the manufacturing process requires a lot of energy, about six tons of CO2, according to some sources, including Volvo1. Building a new 30gw Gigafactory - i.e., one capable of producing 30 gigawatts of lithium-ion batteries - can cost up to £3.5bn, according to some estimates.
There are three main types of EV battery: LFP, NMC and NCA. You can find out more about these battery types here and the workings of batteries generally, here. Lithium-ion batteries (LFP) are used in the biggest percentage of EVs like those found in your phone or handheld device.
What manufacturers have found over the years is that, unlike the power cell in your mobile phone, EV batteries tend to retain their life or ‘capacity’ quite well, even after being recharged thousands of times. Contrary to public opinion, there is much evidence now to suggest that EV batteries may even outlast the ‘useful’ life of the car itself. Nevertheless, residual values for used EVs have proved to be quite challenging in the UK and Europe but have been arguably more dependent on demand/supply dynamics and technological evolution rather than battery life.
Competitive pressure and consumer demand have meant that manufacturers have sought to continually increase the range of successive models. The quest for better range has arguably been driven by the twin consumer concerns of range anxiety and charging infrastructure, rather than any focus on sustainability.
Charge of the right brigade
The driving forces behind boosting range may be the twin, long-term aims of achieving economies of scale and profitability, but sustainability goals are also playing a significant part in battery development.
While some commentators think the pressures faced by the automotive sector over the past three years have diverted attention away from sustainability and towards stark economic survival, much has been going on behind the scenes regarding the circular economy, recycling and repurposing of EV batteries. As sourcing the materials needed, cobalt and lithium chief among them, raises ethical and cost questions, more and more emphasis is being placed on, repairing, repurposing and recycling batteries already in use.
A whole new industry has arisen that runs parallel to the 400 (and counting) gigafactories2throughout the world. While they are focused on the construction of new batteries to supply manufacturers in relative proximity, companies including, Spiers New Technologies (SNT), Li-cycle, Northvolt and Accurec are partnering with manufacturers to repurpose and repair batteries to keep them in use for as long as possible – common sense sustainability. Some companies harvest valuable waste that results from the battery manufacturing process so that it can then be used in recycling. SNT, acquired by Cox Automotive in 2021, focuses on the repair and maintenance of batteries throughout their lifecycle.
The evidence suggests that batteries will get smaller, their kWh will increase, and their performance will be improved upon. Cost is also coming down, due to economies of scale and innovation. Manufacturers are forging new, untypical partnerships with educational and research institutions to uncover better battery solutions.
Companies such as SNT are driven by the overarching desire to minimise the risk of battery failure and to evolve both the maintenance and repair of battery packs. The development of servicing and repair is advancing so rapidly that experts in the field think the day will soon come when a customer takes her EV in for a routine check-up and the focus of that service will be on the battery’s health and its management system.
Find out more about the work SNT does here.
A question of insurance
The issue of making EV batteries more repairable feeds directly into the topic of car insurance, as many commentators think premiums will continue to rise unless manufacturers come up with cheaper batteries that can be maintained or repaired more easily. Repair costs, for EVs generally, are exacerbated by the price and availability of materials, the lack of repair expertise (compared to ICE vehicles) and the complexity and value associated with their structure.
A report this year, by Thatcham Research and Innovate UK2 outlined the variety of challenges preventing greater EV adoption. The report says that most focus has been on range anxiety and infrastructure at the expense of repair pain points and insurance which combine to create a significant barrier to EV adoption.
It adds: “BEV incident claims are currently about 25.5% more expensive than their ICE equivalents and can take some 14% longer to repair.” Thatcham Research data shows that in 2022, 9,400 vehicles were involved in collisions resulting in potential battery damage. This total is expected to be about 260,000 vehicles yearly by 2035. Without change in the form of lower-cost parts, better repair capacity and training, the report concludes, claims costs will likely continue to rise disproportionately.
Some insurers, including John Lewis Financial Services, have reportedly paused the offering of new policies and renewals to EV owners. The move by John Lewis was apparently over “risks and costs entailed”.
The trend of low-mileage EVs being written off with minor damage is also, apparently, growing3. Following many EV collisions, there is often no expertise to fix or assess battery packs, which forces insurance companies to simply write off cars. And that inevitably means higher premiums.
While it’s clearly the easiest route for the insurance company to take, this is an issue that will only be resolved with time and, presumably, one that can only be helped by manufacturers pouring more money into research and making batteries more ‘fixable'.
Battery passports
As the number of EVs on the world’s roads grows at a rapid rate, so too will the need to monitor the whole story of the battery, where they were made, what materials were used and their condition status.
Already deep in development, battery passports are set to play that role in the coming years. They are a digital record of the power source’s lifecycle, from its essential ingredients to its eventual disposal. It will contain information about its origins and environmental footprint.
It’s expected that these digital records will become compulsory in the European Union in 2027 (for every new battery more than 2kWh in size). In the US and UK, similar measures are currently being consulted on.
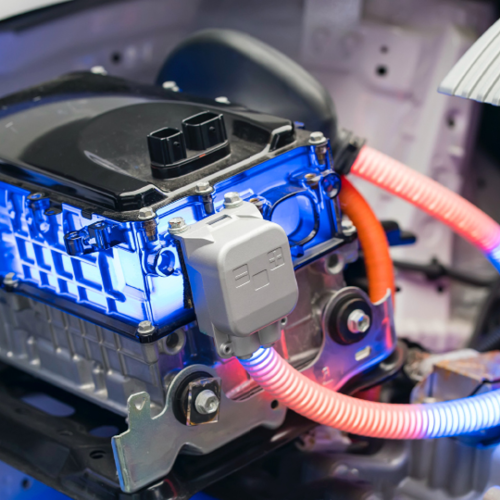
The strict regulations associated with battery passports point to a culture of stringency that will direct how manufacturers operate within the EV space. A high percentage of EV battery materials, around 90%, are recyclable4. Countries producing the batteries will be faced with greater responsibility for them as the passport means it can be tracked right through its lifecycle.
Fundamentally, the battery’s usage and energy consumption can be monitored, meaning greater control and, therefore, there’s a more rigorous way to make the industry producing it more ‘circular’.
Black mass and the circular economy
The stripping and recycling of used batteries, as an industry, is in its infancy but is still big business. By 2030, according to some sources, the global EV battery recycling industry is expected to be worth $19.3 billion.
The recycling process involves disassembling the battery, before extracting and separating the precious materials inside, such as lithium, cobalt and nickel, to make a valuable mixture of valuable metals called black mass. It is then further processed to filter out the valuable metals which can then be used to manufacture new EV batteries.
Manufacturers are keenly invested in this growing area, as it means a surefire route to meeting sustainability goals. Although it doesn’t always reduce battery manufacturing costs, it certainly reduces the cost of raw materials while helping to meet the demand for EV batteries. Having control over vital ingredients in their supply chains is almost priceless.
State of things to come
Manufacturers are seriously invested in getting the best bang for their buck when it comes to battery production and the evergreen importance of increasing range is undeniable.
Technological advancements are key then, which is why the announcement earlier this year from Toyota’s chief technology officer, Hiroki Nakajima, was big news. He revealed that the Japanese giant, the world’s second biggest in revenue terms, would be introducing the world’s first solid-state EV battery (SSB) in 2027/2028.
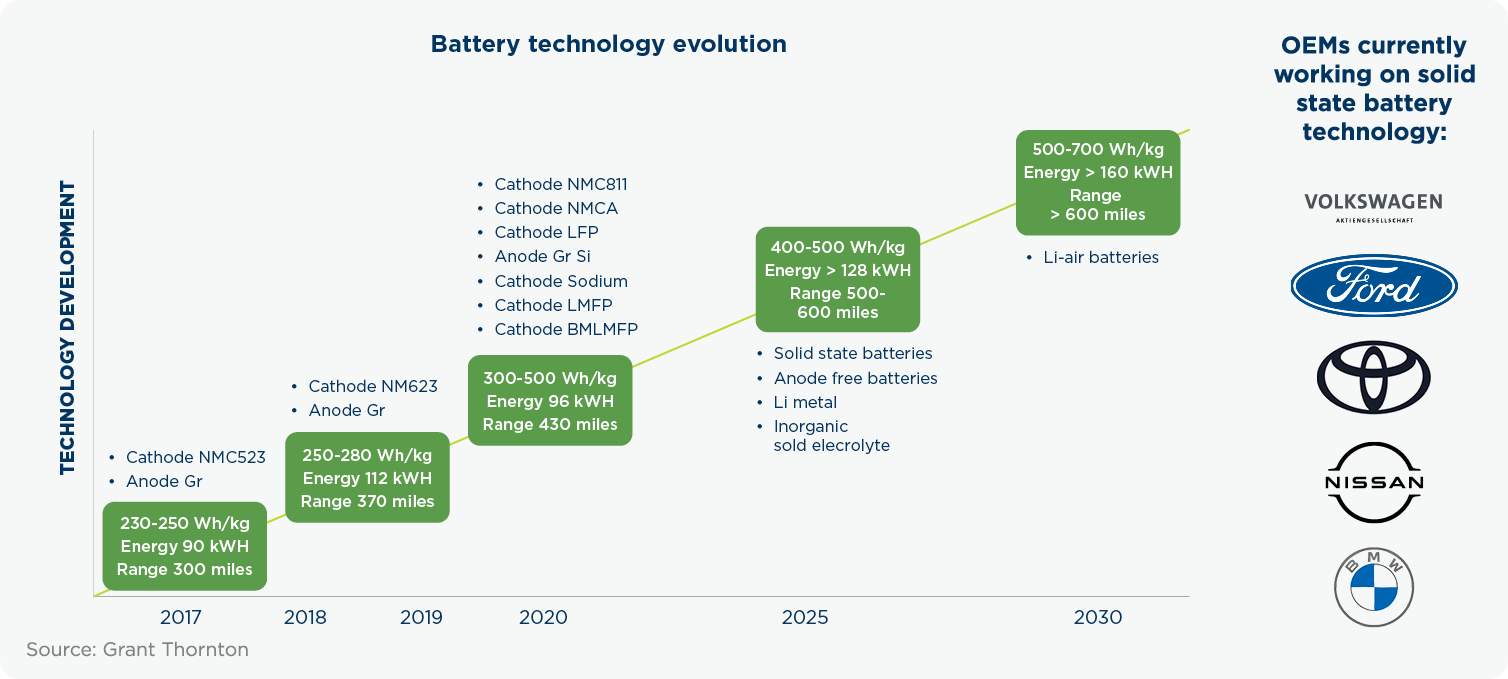
With more than 1,000 SSB battery patents (more than any other manufacturer), Toyota says it has many similar innovations coming down the line.
SSBs consist of solid electrolytes as opposed to liquid (in lithium-ion batteries). Toyota claims their prototypes are about the size and thickness of a thin spiral notebook. They also say the power packs are the answer to many of the problems facing EVs run on lithium-ion, including range, charging times and safety.
Several other manufacturers are in the race to commercialise SSBs. Honda announced last year that it had developed a polymer fabric that could extend the life of the SSB. It will go public with the invention in 2028.
SSBs are, according to some, the industry’s Everest, as range and charging times remain two of the biggest obstacles to widespread consumer adoption.
Swap shop
Chinese EV maker Nio has developed a battery-swapping system called Power Swap. The Shanghai-based company has built a network of more than 1,300 swapping ‘stations’ in China and opened its first European station, in Norway, last year. It plans to extend it to other countries too. These stations allow Nio drivers to quickly replace (temporarily or permanently) a depleted battery with a fully charged one in a matter of minutes. Nio thinks that switching the battery pack in minutes will be much more preferable than having to wait on a vehicle charging. Tesla is reportedly working on a similar system in the US. Ample is a California-based company working on a battery-swapping system for commercial vehicles. It has already built a network in the Golden State.
As EV uptake increases, such swapping stations will become more commonplace across the world, as they provide a potentially convenient choice for EV drivers who don’t have time to hunt down or wait at a public charging point. They are likely to play a significant role in the adoption of EVs and only hint at the strides that are being made in battery technology.
Better living through chemistry
Some of the finest scientific minds in the world have been deployed by manufacturers to help make batteries last longer and retain their power capacity with greater efficiency.
The number of relevant developments in the scientific world are copious but include the use of new materials in battery cathodes and anodes, the positive and negative electrodes of a battery respectively. When a battery is charged, lithium ions move from the anode to cathode. When the pack is discharged, the ions move back in the opposite direction. Their movement is what generates electricity.
Several companies in the US and Europe are developing silicon anode material for use in batteries that will have a much higher energy density than those currently in use. In short, they provide a longer range and could, eventually, help reduce the cost of EVs. Several large manufacturers, including Porsche, VW, Mercedes, BMW and Hyundai are set to deploy the innovation in the coming years.
There is much to unpick when it comes to the most expensive part of an EV and the element that decides, crucially, both its range and the length of a vehicle’s useful life. Manufacturers are ploughing billions into research and have already had success in making batteries more durable, smaller, lighter and more powerful. A new industry has emerged to manage, repair, recycle and repurpose them and software ecosystems have arisen to track batteries from the cradle to the grave.
From a sustainability standpoint, the important work that’s going on to improve chemistries and fortify recycling processes is not being done purely to boost EV sales. The level of collaboration we are seeing between car manufacturers and the keenest scientific minds illuminates a transparent mission to minimise waste, conserve resources and drive lasting efficiencies in production.
PERSPECTIVES
References
- Emission free Volvo L25 Electric proves valuable partner in waste and recycling
www.volvoce.com/europe/en/about-us/news/2023/emission-free-volvo-l25-electric-proves-valuable-partner-in-waste-and-recycling/ - Over 400 gigafactories in 2030 pipeline, but overcapacity fears loom
source.benchmarkminerals.com/article/over-400-gigafactories-in-2030-pipeline-but-overcapacity-fears-loom - Electric Car Revolution Threatened By Excessive Insurance, Repair Costs – Reporthttps://www.forbes.com/sites/neilwinton/2023/07/04/electric-car-revolution-threatened-by-excessive-insurance-repair-costsreport/
- Raw material recovery through recycling: what happens to the ID. Battery?
www.volkswagen.co.uk/en/electric-and-hybrid/sustainability/electric-car-battery-recycling.html
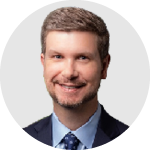
Jonathan Smoke
chief economist, cox automotive INC.
The future of EV battery production, recycling and repurposing…
The battery is the heart of an electric vehicle. As the demand for EVs grows, so does the demand for high-quality, energy-efficient batteries. This demand has increased for battery manufacturing and remanufacturing facilities. Cox Automotive employs thousands related to the remanufacturing, reuse, and recycling of the EV battery lifecycle across multiple locations in Belleville, Mich., Las Vegas, Oklahoma City and Ede in the Netherlands. Brian Skalovsky, Director of Battery Recycling for Cox Automotive, sees the development of environmentally friendly battery recycling methods as an ethical imperative. "This is about being part of something special and leaving the next generation a better planet", said Skalovsky.

Jürgen Stackmann
Director Future Mobility Lab @Uni St.Gallen, Lecturer @HfWU Geislingen
The future of EV battery production, recycling and repurposing…
The gold rush is just about to start. To keep it going and keep it green circular economy thinking and planning need to be an integral part of the complete industrialisation of the EV business – right from the start. In parallel to full industrial scaling of EV manufacturing, the industry needs to start seeding an industrial regional repair, repurposing and recycling industry to secure regional material supply for the future and ensure an environmentally sustainable footprint.
We are still in the early days of this industrial second cell life industry in Europe. Still, circular thinking has, I believe, a place in OEM strategy and pilot activities already exist. Renault's activities in France to re-use a production site for vehicle refurbishing is a good example. Another example is Volkswagen Group's pilot activities to research and pilot industrial battery cell material in Salzgitter.
Latest estimates suggest that a recycling quota of over 90% of battery cell materials is within reach – full industrial scale will only be possible about 10 years after the introduction of the first wave of BEV vehicles kick-off around 2020. These activities must be organised nationally or regionally. Battery pack transportation costs are a significant part of the value chain (and efforts to reduce the CO2 footprint) – will be a significant business opportunity for specialised companies in the coming years.
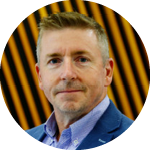
Mathew McAuley
Director of Strategy & Marketing, Cox Automotive Australia
The future of EV battery production, recycling and repurposing…
There’s clearly a push to diversify the global EV supply chain away from China, which remains dominant. This manifests as, for example, US industrial policy under Biden and the establishment of battery hubs – there’s even talk of production in Australia value-adding onto domestic minerals using local know-how.
Keys to re-use and resale are finding a way to offer compelling customer-facing battery health scores and scaling Australian businesses focusing on battery refurbishment, reuse and recycling, for example, Melbourne’s Infinitev. When it comes to this stuff there’s lots of talk but little action.
With battery module refurbishment and recycling beset by high costs and a lack of regulation, legislators probably need to play a key role in creating an industry around this issue.
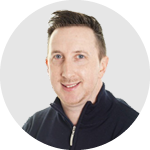
Matthew Davock
Director of Manheim Commercial Vehicles, Cox Automotive
The future of EV battery production, recycling and repurposing…
The coming transition presents a dilemma for recyclers because the logistics and business models for recycling scrap and end-of-life batteries are very different today versus what is likely to happen in the future. The development of second-life applications and recycling processes for EV batteries needs to advance more rapidly to help mitigate future residual value risks for LCVs.