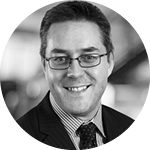
Owen Edwards
HEAD OF DOWNSTREAM AUTOMOTIVE

12 min read

Automotive manufacturing is on the cusp of change. In 1934, Citroen was the first company to unveil the integrated unibody vehicle: the Citroen traction Avant, which was produced for more than 23 years, selling 760,000 vehicles. It was the first iteration of the monocoque chassis – an integrated body and chassis which formed spot welding and deeply stamped steel sheets into a structural cage which included sills, pillars and roof beams. Other components of the vehicle are hung from this structure to construct a complete vehicle. Most manufacturers are using, or have used, this process to produce passenger cars and light commercial vehicles.
However, BEVs (Battery Electric Vehicles) are changing the production environment. With the increased cost of manufacturing BEVs – the high cost of batteries and the requirement to reduce the retail price of vehicles to make them more comparable with ICE vehicles – the BEV manufacturing process must become more cost-efficient. The monocoque process of manufacturing is common among most OEMs and this legacy process has been used successfully for over 50 years. However, Tesla and many others have announced that they will be changing their BEV manufacturing processes. With the improvement in new 9,000-tonne gigacasting processes developed by Idra Group in Italy, which produces a sub casting for both the front and rear of the vehicle. Tesla has changed its manufacturing process, for its model Y, from monocoque to an “unboxing process”.
The unboxing process enables the vehicle to be constructed in a modular way and more efficiently. Also called Global Automotive Modular Evolution (GAME), such a process enables the vehicles to be constructed in modules as can be seen below. This consists of a front, rear, battery and floor section, with sides and roof being added as the final piece of the jigsaw (see diagram).
The Unboxed Process or GAME
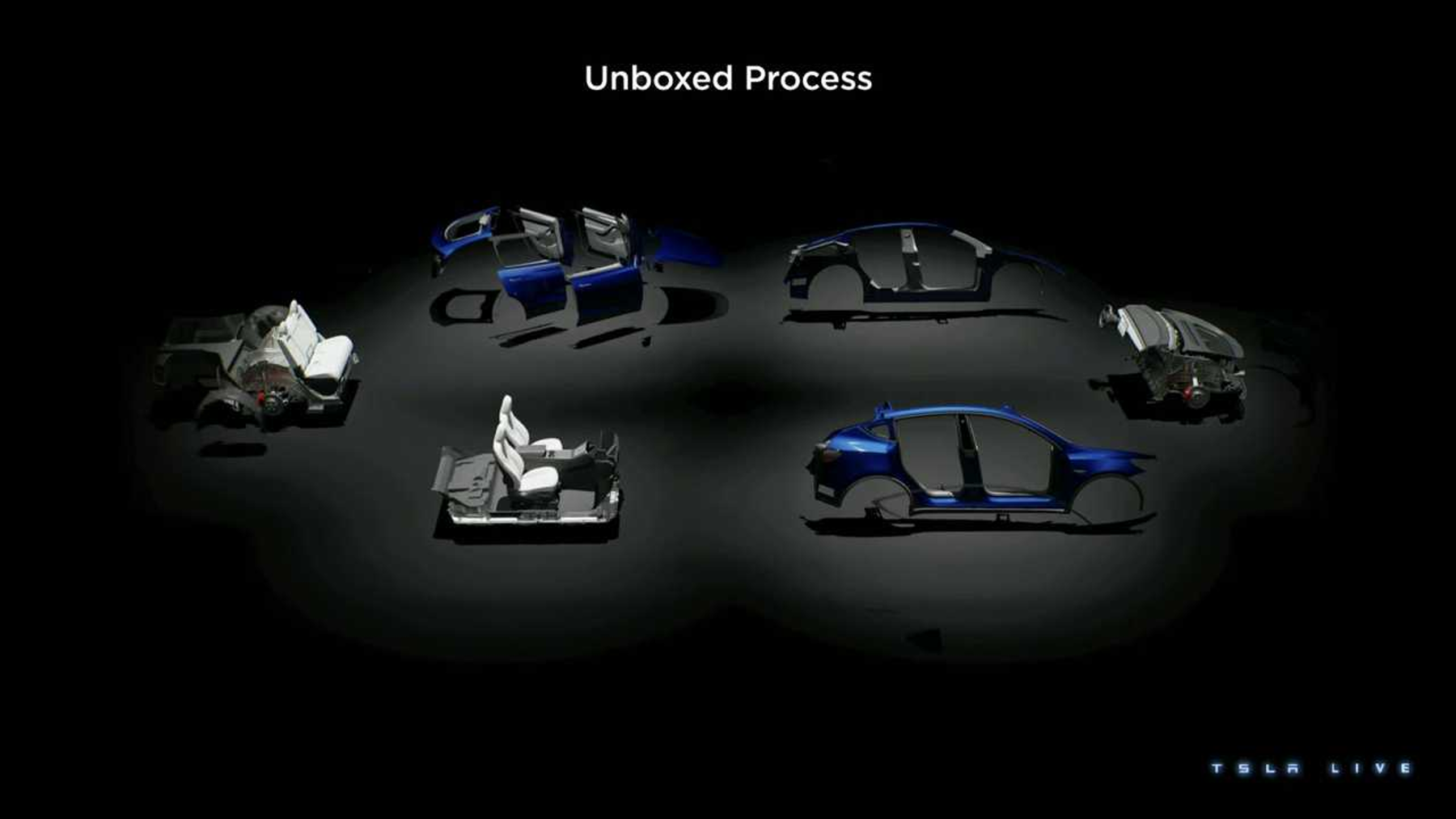
Source: Telsa Live 2023
As can be seen, one of the core areas of this process is the use of gigacasting at the rear and front of the car. This can be seen in the picture below, with the relevant sections which highlighted in blue.
Diagram of the Tesla Gigacasting in the model Y
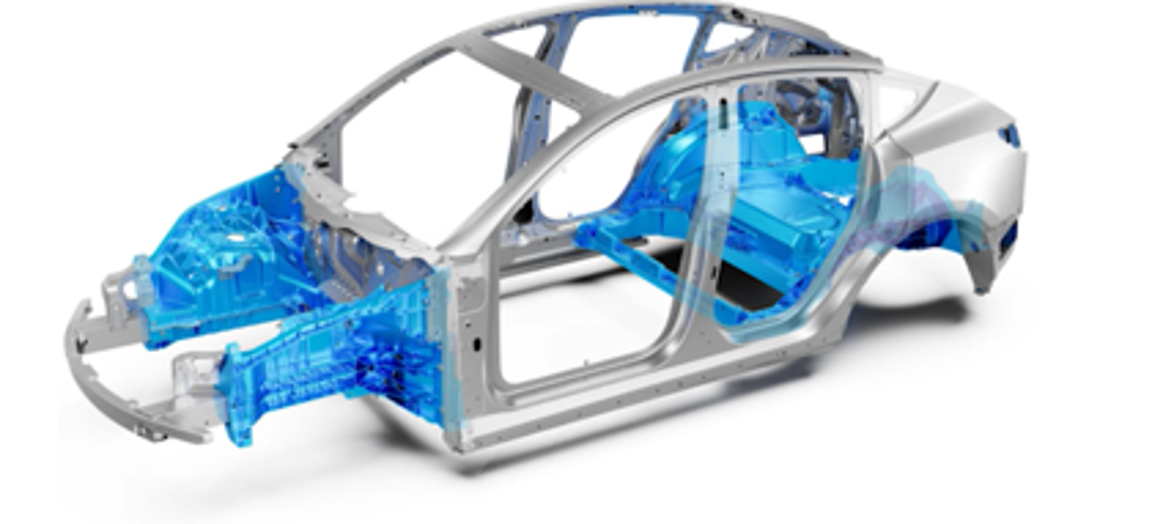
Source: Telsa
The use of gigacasting at the front and the rear of the vehicle allows Tesla to not only manufacture the front and rear in a number of independent modules which can then be brought to one central assembly plant, but it also removes over 100 stamping and welding steps in the production process, which in turn reduce the vehicle’s production cost and makes the vehicle lighter.
Tesla can attach these gigacastings – front and back – to the vehicle’s battery which becomes the central part of the chassis. With the battery and gigacastings now attached to each other, before the sides of the vehicle are secured to the battery and gigacasings, the OEM uses robots to install the interior of the vehicle, carpets, seats dashboard etc. Such a process allows the OEM to speed up production processes and further reduce costs as there is less labour used.
Tesla’s unboxing process
Source: Telsa Live 2023
Tesla believes that the gigacasting and modular approach to constructing a vehicle could reduce their factory carbon footprint by approximately 40% and total cost of production by 50% (source Tesla Live 2023).
However, if we look at this from the opposite perspective, Tesla would reduce both its costs and capital investment in production processes. This includes building a battery electric vehicle (BEV) for $25,000. Tesla has indicated that such a vehicle will be the Model 2 (Project Redwood), a compact SUV. The price of a small SUV at $25,000, with some pundits in the UK suggesting that it would be £25,000 (not a straight dollar to sterling swap) which would create a vehicle which, in cost terms, is broadly in line with a current ICE SUV.
The market share of BEVs in the UK has stalled at c16%-18% of total new vehicles registered in 2023. The high price of BEVs has been one of the core catalysts for consumers not purchasing BEVs. However, a much lower priced BEV such as the Tesla Model 2 and increased legislation caused by the UK ZEV Mandate could once again ignite demand for BEVs. Tesla has not provided an exact launch date for the Model 2, but production is expected to start in the second half of 2025.
What remains unclear is how legacy OEMs will react to the Tesla Model 2 priced at US$25,000. Some OEMs are already starting their own GAME processes and will be able to compete in the future with Tesla, however we have no certain outlook when this will be.